Harper’s extensive experience across a range of materials gives us the unique ability to deliver the ideal thermal system for battery materials processing to enable the customer’s success in their manufacturing operations. As development of materials for energy devices such as battery cathodes, capacitors and super-capacitors are progressing rapidly for cutting-edge applications demanding power sources be smaller, lighter and more efficient, manufacturers need systems to meet the challenge.
Harper has designed advanced furnace and kiln systems for some of the world’s leading energy storage material companies. We focus on processing in controlled and specialty atmospheric environments and at temperatures from 300 to 3000°C, and offer designs with gas, electric, and microwave heating. Harper’s expertise covers calcination, graphitization, carburization, controlled oxidation, oxide reduction, purification, pyrolysis, drying, reduction, solid-solid reaction, gas-solid reaction, metalizing, debinding, waste remediation and more.
Many companies on the cutting edge of research in new energy device materials need assistance in developing and fine tuning their thermal regimes. At Harper’s Technology Research Center, customers can utilize a number of onsite furnaces and kilns, and have Harper’s expertise at their disposal to work through their process development and process optimization. Harper also provides a variety of additional analytical services such as gas analysis (critical to ensuring compliance with environmental regulations) electron microscopy, XRD, BET, and other thermal and elemental analysis.
Technology Solutions for Energy Device Materials
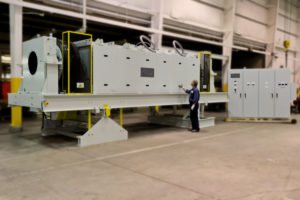
Many applications require performance and safety that is only achieved by maintaining ultra-high purity. Harper’s Rotary systems operate from 500 to 3000°C and support these high purity applications from beginning to end: material in-feed valves and feeder, high-heat reactor tube, product cooling tube, and material discharge valves and collection. We have the experience to engineer these components to achieve a chemically inert environment all while maintaining a gas-tight and dust-tight system for your advanced material.
Learn more about Rotary Furnaces.
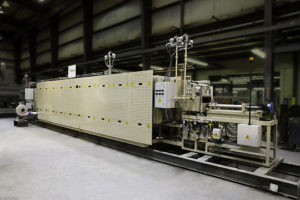
As many thermal processes for energy device materials require exacting conditions, our innovative design enhancements consider the delicate pressure control within the system to provide accurate direction of the atmosphere flow path in the kiln. This facilitates evacuation of volatiles and optimizes atmosphere uniformity. Additionally, Harper’s unique gas curtain technology provides zone-to-zone atmosphere definition under specific conditions.
Learn more about Pusher Furnaces.
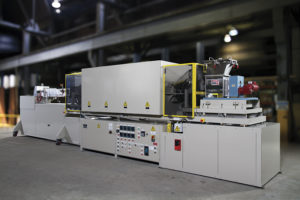
Learn more about Belt Conveyor Furnaces.