Materials for energy generation applications are becoming more critical as society looks towards alternative means of power beyond fossil fuel-based methods. Harper has been a critical partner for nuclear fuel processing furnaces and kilns for decades to companies developing new energy generation technologies and optimizing their existing operations.
Since 1957 when the first nuclear fuel sintering furnace for General Electric was produced, Harper has become the world’s leading provider of customized systems offering a range of advancements in energy efficiency, temperature uniformity, maintenance, and safety control. Typical applications for nuclear fuel processing include:
- Sintering UO2 pellets for reactor fuel rods
- Oxidation UO2 pellets, swarf, and powder to U3O8
- Denitration of Uranyl nitrate
- Hydroflourination of UO2 pellets
- Waste remediation
Harper’s engineering practices provide for robust, efficient designs. For nuclear fuel processing, reliability is of the utmost importance, which is why our energy efficient systems have well proven insulation packages catered to the process and furnace requirements. Harper’s furnaces and kilns can include baffles and other features to reduce end tube radiation loss to improve the energy efficiency. Rotary systems often provide great energy efficient value since there is no carrier load which requires energy to heat and cool the boat or product tray.
As the utilization of energy generation materials continues to grow, Harper aims to enable companies in the optimization of their production processes. Our dedicated Pulse™ service team’s experience in rebuilds, retrofits, upgrades and process analysis/optimization can help drive improvements for a customer’s operational efficiency and effectiveness. As always, we aim to devise a turnkey solution with a range of offerings including gas treatment and handling and fully integrated control systems to provide a total package.
Technology Solutions for Nuclear Materials
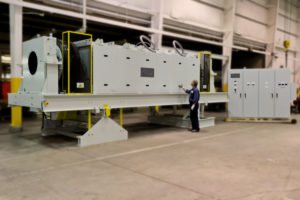
We also offer expertise in designs for both waste remediation and material dilution. During nuclear fuel pellet production there are several operations that produce waste, including swarf from pellet grinding operations and broken pellets. These waste products are oxidized from UO2 to U3O8. This material is then re-introduced into the production of nuclear fuel. We also offer expertise to dilute highly enriched nuclear material into non-enriched material, designing systems used to convert highly enriched UO2 to U3O8 and then reprocess it into nuclear fuel.
Learn more about Rotary Furnaces.
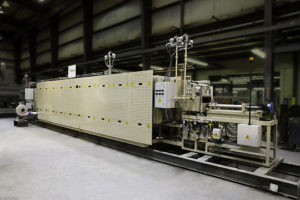
Our Pusher furnaces and kilns provide high temperature capability required with hydrogen atmosphere and dewpoint control for sintering processes. They are typically molybdenum element heated with high alumina oxide based refractory. These sintering furnaces are highly reliable and have remarkable longevity, with many Harper sintering furnaces in operation for over 25 years.
Learn more about Pusher Furnaces.