Harper is trusted worldwide for high temperature powder processing furnaces for powders and granular materials, including inorganic chemicals, catalysts, phosphors and powdered metals. Our batch and continuous furnaces and kilns for these materials focus on processing materials in controlled and specialty atmospheric environments and at temperatures from 300 to 3000°C.
Our experience designing custom batch or continuous thermal processing systems for a variety of applications producing aluminas, carbon/graphite, silicas, titanates, tungsten, cobalt, iron, zinc, quartz, molybdenum, zirconia, and more. Harper delivers innovative powder processing furnaces for these materials with a focus on controlled and specialty atmospheric environments. We have breadth and depth of expertise that covers gas-solid or solid-solid reactors providing calcination, graphitization, carburization, controlled oxidation, reduction, purification, pyrolysis, metalizing, debinding, waste remediation, and more.
Unlike other furnace manufacturers, our range of furnace technologies and knowledge of an array of materials allows us to incorporate more advanced features to optimize your process. Harper’s experienced engineering team utilizes our technology toolbox to include patented features like superior seals, mixing techniques, and enhanced flow designs for the most efficient solution possible.
As every material is unique, every powder processing furnace is as well. We don’t shoehorn a standard line of products to fit our customers’ requirements. Our passionate team uses our building blocks to deliver first-of-a-kind solutions for the customer’s distinctive needs in their powder production process while considering the most efficient and effective construction possible. Our focus is on precision control over temperature, purity, atmosphere, material flow and residence-time distribution required for consistent and uniform material processing.
Technology Solutions for Powders
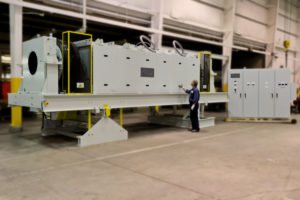
Many applications require performance and safety that is only achieved by maintaining ultra-high purity. Harper’s Rotary systems consider these high purity applications from beginning to end: material in-feed valves and feeder, high-heat reactor tube, product cooling tube, and material discharge valves and collection. We have the experience to engineer these components to achieve a chemically inert environment all while maintaining a gas-tight and dust-tight system for your advanced material.
Learn more about Rotary Furnaces.
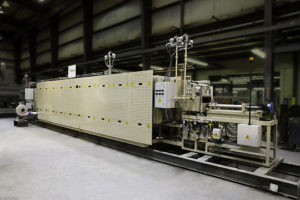
As many thermal processes for powders require exacting conditions, our innovative design enhancements consider the delicate pressure control within the system to provide accurate direction of the atmosphere flow path in the kiln. This facilitates evacuation of volatiles and optimizes atmosphere uniformity. Additionally, Harper’s unique gas curtain technology provides zone-to-zone atmosphere definition under specific conditions.
Learn more about Pusher Tunnel Furnaces.
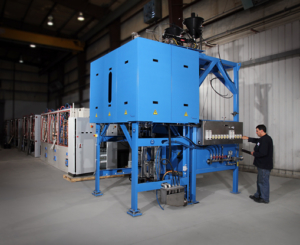
One of many advanced design features, our system’s specialized material movement limits the potential for overheating problems, such as melting/sublimation, sintering or excessive grain growth. In addition to the container-less nature of the design, thermal transfer between product and reactants significantly improves the power efficiency of the unit. Our Vertical system limits heating and cooling requirements to the process material only – containment remains at temperature and the process material moves through it - resulting in better heat and mass exchange between products and reactants for improved efficiency.
Learn more about Vertical Conveyor Furnaces.