Like our customers, Harper is perpetually on the cutting edge of our industry. Both academic and industrial organizations trust Harper International for high performing thermal processing equipment, including our high temperature kilns, furnaces, and ovens for developing advanced materials like Graphene, Activated Carbon, Carbon Gel, and other advanced carbon materials in controlled and specialty atmospheric environments and at temperatures from 300 to 3000°C.
Graphene is an exciting new material that presents extraordinary possibilities for advancements in electronics, batteries, medical applications, and more. As the market evolves and matures, Harper aims to be a partner to the industry, supporting the optimization and refinement of process parameters that ensure capacity and quality requirements are achieved throughout the scale up and commercialization stages.
At our own on site Technology Research Center, customers can utilize Harper’s multiple furnace systems and tap into the expertise of our team for their process development and process optimization. This approach helps de-risk and ensure the process is fully refined for commercial scale-up prior to investment in production scale thermal processing equipment. Harper also provides a variety of additional analytical services such as gas analysis (critical to ensuring compliance with environmental regulations) electron microscopy, XRD, BET, and other thermal and elemental analysis, to support customer’s expanded needs.
Technology Solutions for Carbon & Graphene
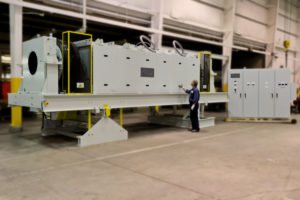
Many applications require performance and safety that is only achieved by maintaining ultra-high purity. Harper’s Rotary systems consider these high purity applications from beginning to end: material in-feed valves and feeder, high-heat reactor tube, product cooling tube, and material discharge valves and collection. We have the experience to engineer these components to achieve a chemically inert environment all while maintaining a gas-tight and dust-tight system for your advanced material.
Learn more about Rotary Furnaces.
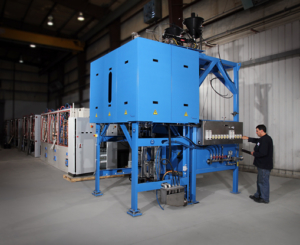
One of many advanced design features, our system’s specialized material movement limits the potential for overheating problems, such as melting/sublimation, sintering or excessive grain growth. In addition to the container-less nature of the design, thermal transfer between product and reactants significantly improves the power efficiency of the unit. Our Vertical system limits heating and cooling requirements to the process material only – containment remains at temperature and the process material moves through it - resulting in better heat and mass exchange between products and reactants for improved efficiency.
Learn more about Vertical Conveyor Furnaces.
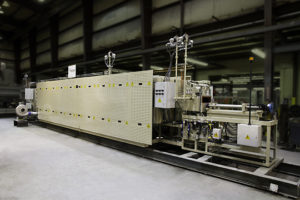
As many thermal processes for energy device materials require exacting conditions, our innovative design enhancements consider the delicate pressure control within the system to provide accurate direction of the atmosphere flow path in the kiln. This facilitates evacuation of volatiles and optimizes atmosphere uniformity. Additionally, Harper’s unique gas curtain technology provides zone-to-zone atmosphere definition under specific conditions.
Learn more about Pusher Tunnel Furnaces.