As the chemical industry expands into more complex and advanced products, Harper thermal processing systems evolve to support the market’s escalating needs. For decades, global companies have trusted Harper as their strategic partner for thermal processing of metal oxides with furnace and kiln technologies to bring new materials to market and scale up their processing rates.
Our experience designing custom batch or continuous thermal processing systems for a variety of applications producing aluminas, carbon/graphite, silicas, titanates, tungsten, cobalt, iron, zinc, quartz, molybdenum, zirconia and more. Harper delivers innovative furnaces for these materials with a focus on processing in controlled and specialty atmospheric environments and at temperatures from 300 to 3000°C. Harper’s expertise covers gas-solid or solid-solid reactors providing calcination, graphitization, carburization, controlled oxidation, reduction, purification, pyrolysis, metalizing, debinding, waste remediation, and more.
The design of a custom Harper system is sparked by understanding the customer’s goals and utilizing our exceptional skilled team to analyze their distinct process requirements for that specific metal oxide. Our multiple Research & Piloting Facility options, deep process and material science knowledge, and custom engineering expertise all support reaching the customer’s thermal processing objectives. In the end, Harper works to devise a complete process line solution with our range of offerings including gas treatment and handling and fully integrated control systems.
Technology Solutions for Metal Oxides
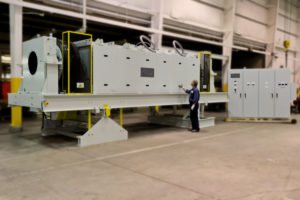
Many applications require performance and safety that is only achieved by maintaining ultra-high purity. Harper’s Rotary systems consider these high purity applications from beginning to end: material in-feed valves and feeder, high-heat reactor tube, product cooling tube, and material discharge valves and collection. We have the experience to engineer these components to achieve a chemically inert environment all while maintaining a gas-tight and dust-tight system for your advanced material.
Learn more about Rotary Furnaces.
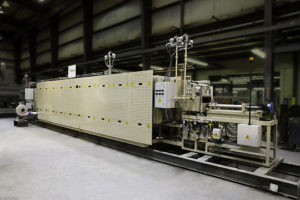
As many thermal processes for metals require exacting conditions, our innovative design enhancements consider the delicate pressure control within the system to provide accurate direction of the atmosphere flow path in the kiln. This facilitates evacuation of volatiles and optimizes atmosphere uniformity. Additionally, Harper’s unique gas curtain technology provides zone-to-zone atmosphere definition under specific conditions.
Learn more about Pusher Tunnel Furnaces.
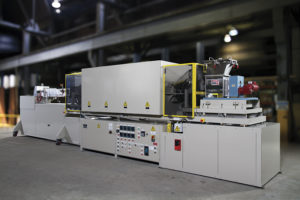
Learn more about Belt Conveyor Furnaces.